Foundry: Aluminum Casting
Aluminum casting is a critical process in the foundry industry, allowing for the creation of complex and detailed metal parts used across various sectors. This process involves melting aluminum and pouring it into a mold, where it solidifies into the desired shape. Aluminum casting is highly valued for its versatility, strength, and lightweight properties, making it ideal for applications in automotive, aerospace, construction, and consumer goods. The foundry industry continuously innovates to improve casting techniques, ensuring higher quality and more efficient production, ultimately contributing to the advancement of modern manufacturing.
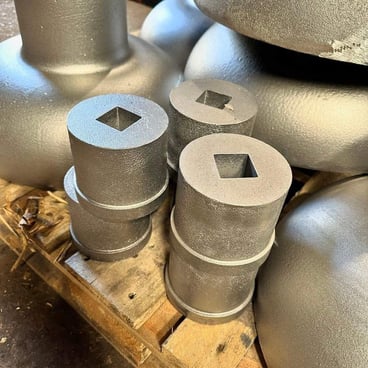
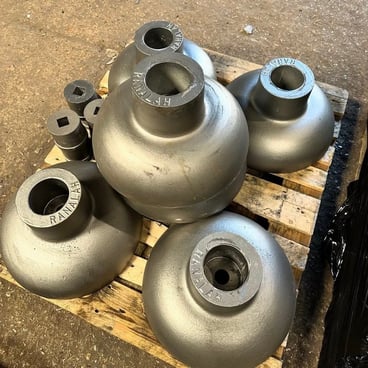
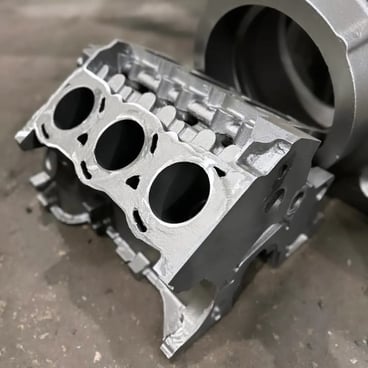
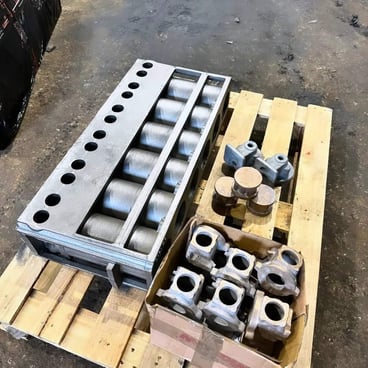
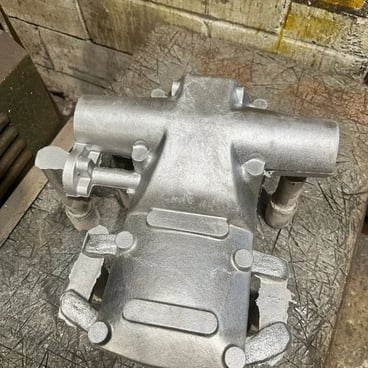
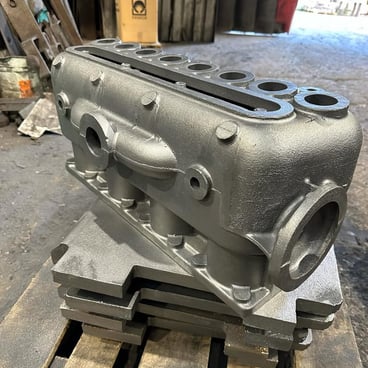
Challenge:
One of the primary challenges in aluminum casting is achieving high precision and quality in the final product. Aluminum's properties require careful control of temperature and casting conditions to prevent defects such as porosity, shrinkage, and incomplete filling of the mold. Additionally, the environmental impact and energy consumption associated with aluminum casting pose significant challenges for foundries striving to maintain sustainable practices.
Our Solution:
To address these challenges, foundries are adopting advanced techniques and technologies. Improved mold design and the use of computer simulations allow for better prediction and control of the casting process. Innovations in cooling methods and the use of high-quality alloys help mitigate defects and enhance the mechanical properties of cast aluminum parts. Furthermore, implementing recycling programs and energy-efficient practices reduces the environmental footprint, ensuring that aluminum casting remains a sustainable option for modern manufacturing needs.